Ultimate Guide to Gate, Ball, and Butterfly Valves
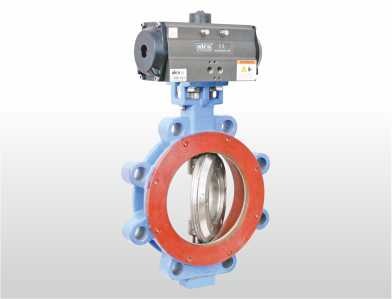
The selection of the right valve for a specific application is crucial when designing a process system. The article will examine the gate, ball, and butterfly valves and the differences between them. By understanding how each type of valve differs and how it will interact with your setup, you can choose the one that best fits your needs.
A valve is one of the most common components found in most industrial sectors, as they are an integral part of piping systems that convey liquids and gasses. Flow control valves regulate liquid or gas flow by permitting it to start and stop, and they must function adequately to prevent leaks and unwanted discharges. In addition, they can use to route flows or isolate parts of the piping system for maintenance or monitoring.
Valve sizes and configurations vary, but their sole purpose is to regulate and control the flow of gas or liquid in the pipe. This article compares the three most common types of valves: gate valves, ball valves, and butterfly valves. Defining each component, exploring what each type of tool can do, and exploring what makes them effective, reliable tools will be our first step.
What is a gate valve?
Gate valves act as gatekeepers, as their name implies. Accordingly, the term originated from the closing component of the valve sliding into the flow to cause shut-off, thus functioning as a gate. On a threaded stem, they have a flat- or wedge-shaped gate, and the gate plates move parallel to the stem.
A closed gate moves into the flow path and seats into a cavity opposite the stem, creating a seal. Upon opening, it completely blocks the flow path, resulting in zero flow obstruction or pressure drop. They are the best suit for high-pressure systems but might require special accommodations in low-pressure systems that need a tight seal. While closed, a low-pressure operation may cause the valve to leak.
Linear motion isolation valves should be kept open or close, as partial opening can lead to damage – they are not using to control medium flow. Gate valves isolate specific areas of the supply network for repairs, maintenance, and new installation activity and reroute flow across the pipeline.
The gate valve is one of today’s most commonly use valves due to its simple design and versatility in low-pressure drop applications. The valves are designe as full-port valves, which means the valve port is the same size as the inner diameter of the connecting pipe. Using a full-bore gate valve, fluid can pass through the pipeline without obstructing or causing a pressure drop. It also makes cleaning the line easier.
Gate valves are generally used for large pipe diameters, from 2″ to the largest pipelines, because they are less complex to design than other large-sized valves.
What is a ball valve?
Ball valves use a rotatable ball with a bore to regulate gas and fluid flow from one opening to another. The opening is aligned with the pipe, allowing the medium to flow freely. Turning the gap off completely stops the flow of the medium since it is perpendicular to it.
In addition to shut-off valves, ball valves are the only way to stop the medium flow immediately. They cannot be immediately redirected. As a result of their robust seal, ball valves are the best use with glasses. They can withstand temperatures up to 350°C and pressures up to 700 bar. Due to their simple structure and compact size, typically ranging from 0.5 cm to 30 cm, these valves are easy to use and repair.
Even after long periods of inactivity, they remain durable and reliable, closing securely even after extended rest periods and continuing to work well. The ball valve is more resistant to contaminated media than other valve types and still provides a good seal regardless of the unclean medium. These features make them an excellent choice in control and shut-off applications, where gate valves are often chosen, however, they are less powerful than other alternatives in throttling applications.
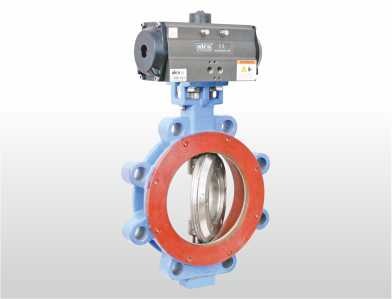
What is a butterfly valve?
Butterfly valves are name after the rotating disc that opens and closes the valve. In pipelines, quarter-turn rotational motion valves are frequently use to shut off flow. Butterfly valves are compose of a disc mount on the valve’s stem, which rotates around the stem to control the flow of fluid through the pipeline. A butterfly valve is fast and easy to actuate, requiring only 90 degrees of movement to go from fully open to fully close.
The disc sits perpendicular to the flow when open, resulting in a slight pressure drop and flow turbulence. Because of this, butterfly valves are not suitable for use in processes containing solids, grit, and other abrasive materials, particularly in waterworks, where they could collect on the disc and prevent a tight seal when closing. Since there is no flow restriction, fluid hammering is more likely than with gate valves. The sudden increase in pressure caused by fluid hammering can damage instrumentation.
Valve applications include water supply, distribution, collection, and pumping stations. They are also widely use in flow isolation. Fabrication ease and compactness are two of their primary advantages over other valve types, resulting in lightweight, cost-efficient products with smaller installation footprints and faster actuation rates.
Structural design
In a gate valve, the plate moves in a straight line parallel to the stem. These lightweight valves feature a flat bottom seat gate, precision casting valve bodies, and integral glue coatings. Gate valves are shut-off valves that open and close completely to allow unrestricted flow.
The stem and ball of a ball valve turn horizontally. In applications requiring on and off control without pressure drop, they are the best suite. The valves have a long service life and provide reliable sealing during their lifetime, even when they are not in use. As a result, they are more popular as shut-off valves than gate valves.
Compared to gate and ball valves, butterfly valves are small and simple. Due to their lightweight and compact design, they can install in tight spaces. Moreover, the disc has a 90-degree reciprocating rotation capability which facilitates regulating the flow and ensuring a complete, leak-proof shut-off.
Working mechanism
Gate valves are complete on-and-off valves. Gate plates, which regulate the media, can only open or close completely. Because of this, the pressure drop is minimal, and the flow is bi-directional. Its design is wedge-shaped and does not allow for flow regulation. Threaded or flanged ends are use on valves.
Through transmission, the ball valve drives the handle to rotate, causing the ball to pivot perpendicular to the media flow. The valve opens when the ball’s hole lines up with the flow and closes when it is turned 90 degrees by the valve handle. Besides being use for non-slurry applications, ball valves can also use for applications requiring a tight shut-off. In some applications that require media isolation, its ability to open and close immediately makes it essential.
Through a butterfly valve, the disc moves around its axis, allowing complete or partial opening and closing. Therefore, the butterfly valve use for partial isolation and regulated flows. Its primary characteristic is the deflection of the butterfly disc, making it a suitable choice for large diameter applications.
Applications
Gate valves have the lowest pressure drop among all valves because of their robust open and close mechanisms. They offer no resistance to fluid flow, making them unsuitable for controlled applications. Straight-through flow paths minimize erosion and turbulence. Gate valves accumulate almost no media.
Ball valves have an uncomplicated structure and good sealing capabilities. Weight is low, the material consumption is low, driving torque is small, installation size is small, and pressure drop is minimal. Ball valves are ideal for general working fluids such as water, acids, solvents, and natural gas, as well as media with extreme working conditions, such as oxygen, hydrogen peroxide, methane, and ethylene – making them an excellent choice. Low-pressure applications commonly require these valves.
Because of its fast opening and closing speeds, the butterfly valve use for throttling, flow regulation, and adjustment control. However, the pressure loss is greater than the ball and gate valve. When choosing a butterfly valve, the pressure loss and operating temperature limitations should be taken into account.
Also, read Popular Ball Valve Types
Conclusion
There are advantages and disadvantages to using gates, ball valves, and butterfly valves, largely based on the application requirements where they are going to install. Gate valves are typically use in applications that require strict sealing and do not require a frequent operation. Ball valves, on the other hand, are the best suit for systems that require periodic shut-off. Last but not least, butterfly valves are the best choice for throttling, as they take up less space in massive systems.
Aira Euro Automation is the leading butterfly valve manufacturer in India. We offer various industrial valves like ball valves, butterfly valves, plug valves, and pressure reducing valves.